
ms Rode Zee
As I was responsible for the
radio room's layout I got a complaint during the sea trials from the Radio
Officer Vogelaar, who had sailed his entire career on Smit tugs and was
very experienced. His complaint was about the positioning of the console, which
contained all the radio receivers and switching equipment. The console was
positioned abeam meaning that the R/O would face forward when sitting in front
of the console. For a small ship, when meeting heavy weather conditions, it is
indeed an uncomfortable position because of the swaying motions of the ship. One
has to balance the body from left to right all the time which is rather tiring.
I explained that when the console was positioned alongships that then both
windows would have been blocked by the same console which would result in a dark
and gloomy radio room. And also that it is not bad weather all the time.
Vogelaar could not be convinced and would have preferred that position
regardless of this fact. However, things could not be changed any more. Also
another R/O would have different thoughts about the blocked windows.....
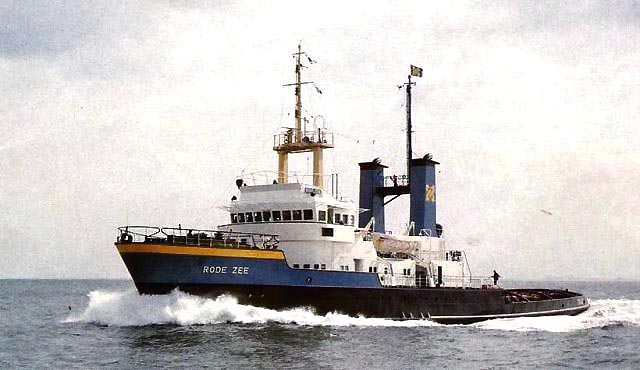
The tugboat ms Rode Zee (Red
Sea) - call sign PGJO - shown in this picture was
the fifth ship by that name. A continuation of a proud Dutch nautical tradition.
The ms Rode Zee owned by Smit International was built in 1968 as number
596 by the Dutch Shipyard 'De Merwede' at
Hardinxveld.
Gross tonnage: 1312
Propulsion: 2 x 6 cylinder Werkspoor diesel engines type 6TM416 nr.2878
en 2879 - 11.000 Hp (5.148 kW). One screw with nozzle and twin
rudders. See picture
and explanation below of the advantages of such a nozzle.
Speed: 15 knots
Dimensions: LxWxH: 68.50 x 12.60 x 6.40 m
1975 A bow thruster was added at the Shipyard Boele's Scheepswerven en
Machinefabriek B.V. at Bolnes
1986 (May) The vessel was transferred to new the new owner Smit Tak
International Ocean Towage & Salvage Company Ltd. at Nassau, Bahamas. The
tugboat was renamed to 'Smit Rode Zee'.
1987 (February) Sold to 'Musi' Triple-S Marine Services Pte. Ltd., Puerto Cortez,
Honduras (as
a tankcleaning vessel).
1988 (October) Towed by the 'Smit Loyd 111' to Kaohsiung to be broken up.
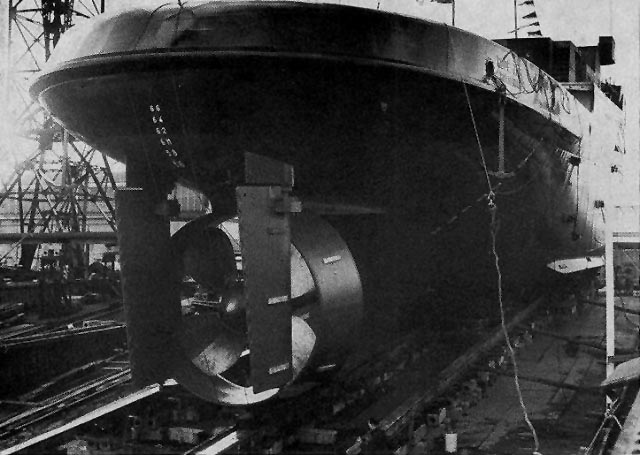
This picture shows the actual
nozzle of the Rode Zee. The majority of such nozzles, either fixed or steerable units, are fitted on tugs. The high bollard pulls being demanded by salvage, coastal towage and
harbours tugs, makes the fitting of such nozzles essential, for to achieve the same bollard pull with an open propeller requires over 45% more power for the same propeller. The
the light coloured white metal parts attached to the rudder and nozzle are
probably part of the ship's self sacrificing cathodic protection system. This
system protects a metal surface of corrosion. Because of the copper screw near
the steel nozzle and rudders corrosion especially in this area can be dramatic.
A cross section of the nozzle
has, in effect, the same shape as an aeroplane's wing but instead of 'lift', a forward thrust is produced. There is no increased thrust on the shafting, the extra thrust is passed through into the ship's hull via the nozzle.
Another advantage for a tug is that a line cannot easily foul up the ship's
screw by accident. Nothing more nightmarish for a tugboat's crew than to be run
over by the towed vessel or object when the screw would get immobilised by such
an incident.
Regarding cathodic protection systems it is may be useful to explain the two
available systems:
Sacrificial Cathodic Protection
: Voltage provided by
sacrificial zinc or aluminium anodes is too high when new, causing high stress
on new coatings and too low when aging, again causing corrosion as coating
deteriorates. Another disadvantage of the sacrificial system is the limited life
time, high reinstallation costs, high drag and fuel use. The advantage is the
lower purchase costs as compared to the impressed current system where
first time investment is relatively high. However, over the life time's span of
a ship this system is more cost effective. Also the corrosion control is very
superior to that of the sacrificial system.
Impressed Current Cathodic Protection: My company Radio
Holland represented and sold the CAPAC impressed current cathodic protection
system which is a much more sophisticated way of corrosion protection and all
done automatically. This protection is provided at optimum ampere levels - too
little and corrosion occurs, too much and coatings may be damaged. With ships,
the optimum amount of amperes is always changing. Ampere requirements increase
proportionately to ship speed, coating age, and oxygen content. The current
provided by the system is automatically and continuously adjusted to meet
changing conditions. Life time of the system exceeds 20 years.
CAPAC systems also feature a silver alloy slip band and silver graphite
brushes to ensure the propeller and shaft are electrically bonded to the hull.
Silver utilised on the contact surfaces provides a low-resistance electrical
connection.